Rotary Joint Service Life
Rotary Joint Service Life
How to increaese the serive life of CHK Rotary Joints:
CHK series is an economically efficient and stable rotary joint, developed and designed specifically for high-performance market requirements. It can be used for water, air, and other media, and is widely used in industries such as steel, rubber, plastics, papermaking, textiles, and chemical fibers. To extend the lifespan of BE-type rotary joints beyond that of competitors, the following three points are key according to COSMAU Technology:
Firstly: Reasonable design, without a doubt.
The BE series products feature a balanced design with flat sealing, split structure, multi-spring internal compensation sealing, pairing of silicon carbide and graphite, providing superior sealing performance. Supported by two imported deep groove ball bearings, they exhibit low rotating torque, wear resistance, and long lifespan.
Secondly: Professional installation surpasses all.
- 1.When installing BE-type rotary joints, ensure that the outer pipe and flange are concentric with the equipment's rotational axis after connection, which can prolong the service life.
- 2.When in dual passage mode, the inner pipe must not exhibit jumping or backlash (rotary-type inner pipes must be securely fixed before assembling the rotary joint). Jumping or backlash can cause fatigue damage to bearings, affecting the service life.
- 3.After installation, do not use water or oil externally for cleaning to avoid damaging the bearings.
- 4.Regarding hose connections: Do not subject the product to tensile forces in the axial or radial directions, as this will increase the bearing load, leading to abnormal bearing damage. Install according to the correct specifications, and if necessary, consult the manufacturer or request professional on-site guidance for installation.
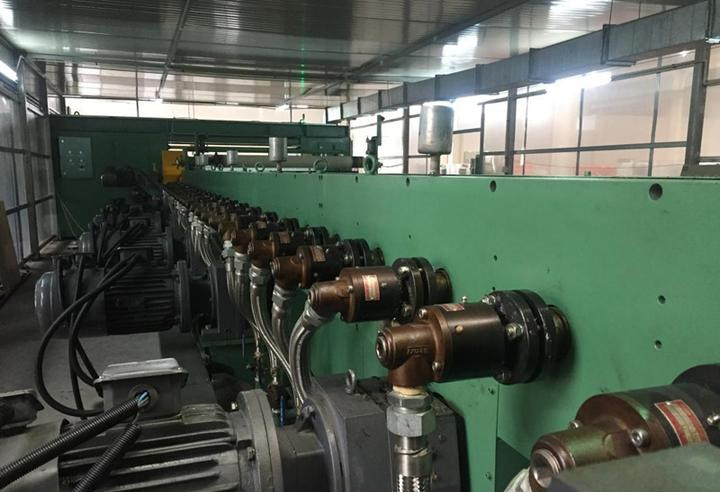
The last: meticulous maintenance adds the finishing touch.
- 1.1.During the handling and installation of BE-type rotary joints, avoid collisions and strictly prohibit hammering, as this can easily cause damage to internal components.
- 2.Keep the rotary joint drum and the inside of the pipeline clean. Pay special attention to new equipment, and if necessary, install filters to prevent abnormal wear caused by foreign objects on the rotary joint.
- 3.When mechanical equipment is in operation, avoid frequent starts and stops. Prolonged shutdown can cause scaling and rusting inside the rotary joint. To prevent jamming or leakage during reuse, it is recommended to remove the rotary joint and apply some grease on the sealing surface to prevent rusting.
- 4.Grease needs to be replenished every six months.